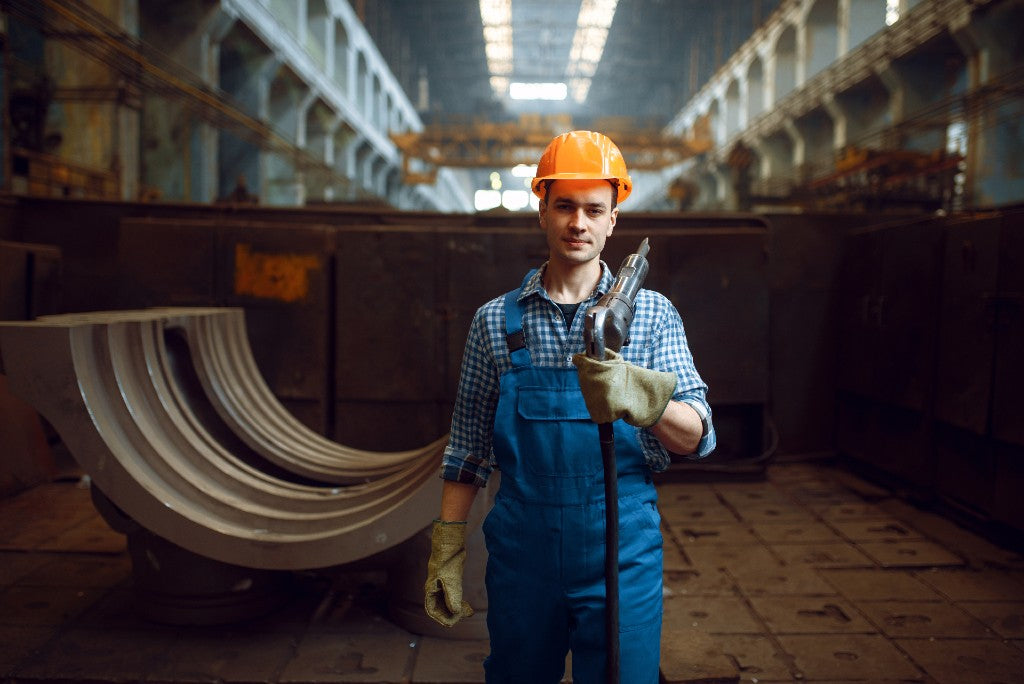
Choosing Whether to Replace Air Tool or Conduct a Pneumatic Air Tool Repair
Whether you're a service technician or industrial operator, spending time diagnosing and troubleshooting air tool problems can help you avoid more complicated issues. Pneumatic tools are vital players in different industrial environments, but their maintenance and repair cycles are easily overlooked. The appropriate care of pneumatic tools is crucial to ensure productivity, efficiency, and operators' safety in every application. Therefore, you need to consider using a reliable Pneumatic Air Tool Repair every time you experience malfunction and breakouts. Although you're too confident with the air tool equipment you just recently purchased, the time will come that it will need a repair or replacement. Hence, you need to know when you should repair or replace a pneumatic tool.
Ensuring Safe Operations by Considering Air Tool Repair or Replacement
Pneumatic tools encounter enormous amounts of stress under challenging industrial environments, so it's not uncommon for breakdowns and failures to occur. Sometimes, it may be the air compressor that has the problem - but there are times when it's the air tool itself. So make sure to practice regular maintenance to avoid problems from worsening over time. If you run a business that uses air tools in your daily operations, it's important to schedule regular air tool service and repairs by experts. By staying on top of necessary air tool maintenance tasks, you can ensure everyone's safety, and your business runs smoothly.
Although air tools are built to stay in good shape for years, they're just like any other piece of industrial equipment—meaning that they can still break down over to,e. For instance, if an operator utilizes used air tools that haven’t been recently inspected or repaired by a professional, they could be at risk of injury during the application. As a business owner, one of your key responsibilities is to always keep your employees safe. You can be confident you're taking every necessary step by making sure you stick to a prompt air tool repair schedule.
Reasons to Get Your Air Tool System Repaired
How often should air tools be replaced? According to a recent survey, air tools are replaced on average of 20 to 30 years when regularly maintained. But how do you know when to repair your air tool and its components? There are many benefits to knowing the right time to repair or upgrade your air tools and improve the quality of your daily production. Read on to learn some of the common reasons to get your air tools repaired by the right professionals.
When Air Compressor Fails to Start
An air compressor failing to start is one of the most common problems that you may encounter. When your air compressor doesn't start, you may shut it down for a minute or two and start it again. In most cases, the air compressor's failure to start is due to a disconnected power cord or deactivated power button. So before starting it, make sure to check the power button and switch first. Aside from power issues, an air compressor can also fail if it lacks the required air pressure level. If this occurs, you may check the cut-in pressure settings and adjust them according to the pressure requirements.
When Air Compressor Fails to Stop
A small compressor for air tools should stop running once the tank pressure reaches the cut-off point. If it fails to stop, there could be a faulty pressure release in the valve or a defective power switch. When the valve fails to release pressure, the machine undergoes over pressurization - and this could seriously damage your air compressor. If this happens, you need to cut the power and replace the valve.
When There are Leaks
If you experience a sudden air pressure drop during an air tool system operation, chances are your air compressor or the connectors have leaks on them. For example, if you deactivate the air compressor when the tank is at its maximum pressure level and notice that the gauge still indicates lower pressure, then you have an air leak. Fortunately, there are so many ways on how you can easily seal the leaks. To determine the leak source, you can try to listen for a hissing sound or run your fingers over the machine and its components and feel if there are air escapes.
Pressure and Flow Problems
Air pressure and flow problems are more complex than the previously mentioned ones. Your air tool system may continue to operate properly, but at some point, the recommended air compressor for air tools can provide too much air pressure or, sometimes, none at all. Besides, the pressure can only reach as far as the necessary PSI level, and not much further. If you notice these issues, all the valves and other components may be compromised. Check these components and have them repaired if they suddenly get damaged.
Get the Right Tool for Your Specific Job Here!
In case you need to replace your old tools that cannot be repaired anymore, Le Lematec Tools is here to help you! Le Lematec Tools is your go-to air tool specialist for all your hand tool, power tool, and accessory needs. Our state-of-the-art manufacturing process ensures high-quality and professional tools that can provide less downtime and loss of productivity for your business. For more details, you may visit us today at https://proairtools.com/ and get the right air tool for any job!