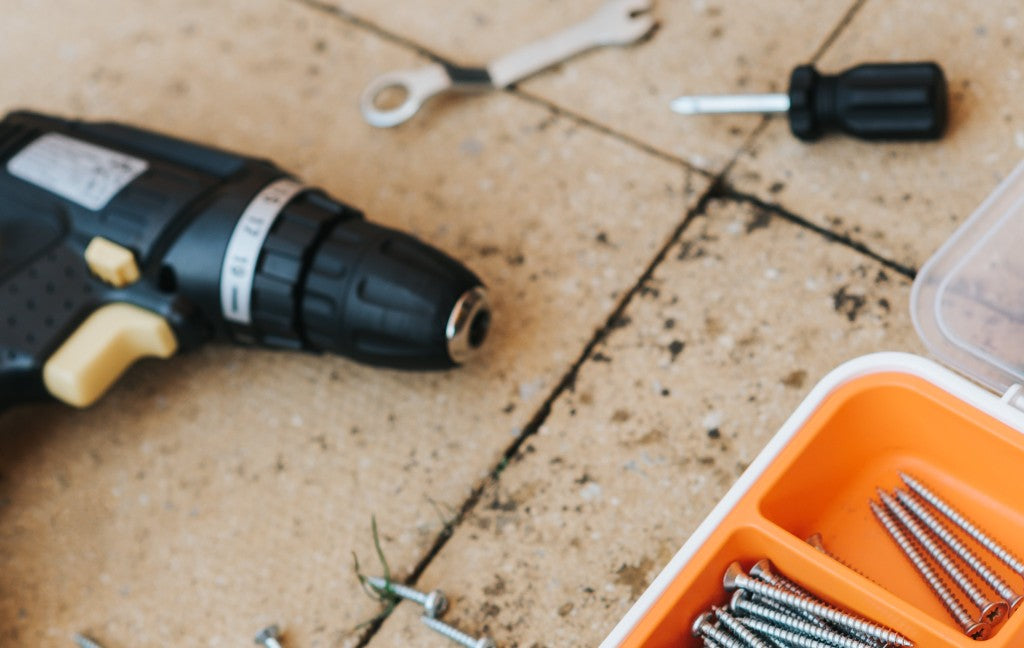
When to Call Professionals When Using Compressed Air Power Tools

Poor-performing Compressed Air Power Tools are pretty common in many home and industrial settings. Over time, air tools may lack torque and even experience gradual delays in operation if not used correctly. This could significantly affect your overall production and can even cost you a lot of money.
Reasons for Air Tool Problems
Most of the time, the primary source of air tool problems is purchasing one that is not suitable for your needs. For instance, you can't easily determine which is which when looking for reliable air tools, especially if it is your first time. Choosing inappropriate designs and models of your air supply systems such as the air filters, regulators, connectors, hoses, lubricators, and fittings can be a problem. These aforementioned air tool accessories are essential in successfully transporting compressed air from the compressor to your working tools. You're lucky if you bought from dependable air tool brands that can allow you to change your purchase. But it doesn’t happen most of the time - hence, make sure to know the required features, size, ad design of air tools and accessories you need before heading to a store near you or ordering online. If these are not selected correctly, the tool may get insufficient or excessive air pressure levels, resulting in inferior air tool performance.
Aside from the incorrect selection, air tool system damage is sometimes a result of overuse. Luckily, there are some easy ways to check and see if your system has problems. You may start by setting up a test using an accurate pressure gauge, quick-connect couplers, and a suitable airline connection. First, place the test air gauge in series with your air tool and check the air pressure. If no air flows to your tool, there should be no pressure drop as well in any air supply gauge that solely feeds the air tool. Next is to operate the air tool, and once there is airflow, you can compare it with the initial pressure before running the tool. If the pressure extremely drops lower than the required level, then you probably have an air system problem. Once you figured out the specific problem, it's time for you to assess if you could fix it on your own or call compressed air tool professionals to help you.
Common Air Tool Problems that Requires Help from the Professionals
Many people are often surprised when they suddenly experience tool malfunction. Buying a good air compressor for air tools is sometimes not enough. Testing helps you determine the problems and can show if your DIY repair or system upgrades have fixed the problem. If not, make sure to call a trusted air tool expert now for an immediate solution.
The following are the common air tools system damage that requires professional help:
If there is air pressure loss.
Loss of pressure affects the system's ability to operate at optimum power, so it ceases to be as efficient or cost-effective, especially if the user attempts to compensate by increasing the pressure from the generator. Most often, pressure is lost between the distribution header pipe and the compressed air-powered equipment. Therefore, all end-use components in-between – connectors, filters, hoses, and regulators – should be of an appropriate size to prevent pressure loss.
If over-pressurization frequently occurs.
Reducing the pressure level in your compressed air system can improve its efficiency and reduce high operating costs in the long run. Unfortunately, many industrial businesses insist on much higher pressure than the required level when running their systems. But this does not always apply. You'll soon realize that higher air pressure levels will not always result in better outcomes.
If there is frequent overheating.
Overheating can occur anytime for several reasons. There are several precautionary measures to consider in avoiding this scenario. Ensure that all vents and fittings are regularly clean and of appropriate size. You may also consider installing a proper ventilation system in the room where it is housed. However, there are some cases when overheating is a result of defective tools. So rather than spending time cooling an overheated compressor to run air tools every after use, make sure to call an air tool expert that can examine the cause of the problem.